Why Electric Conversion?
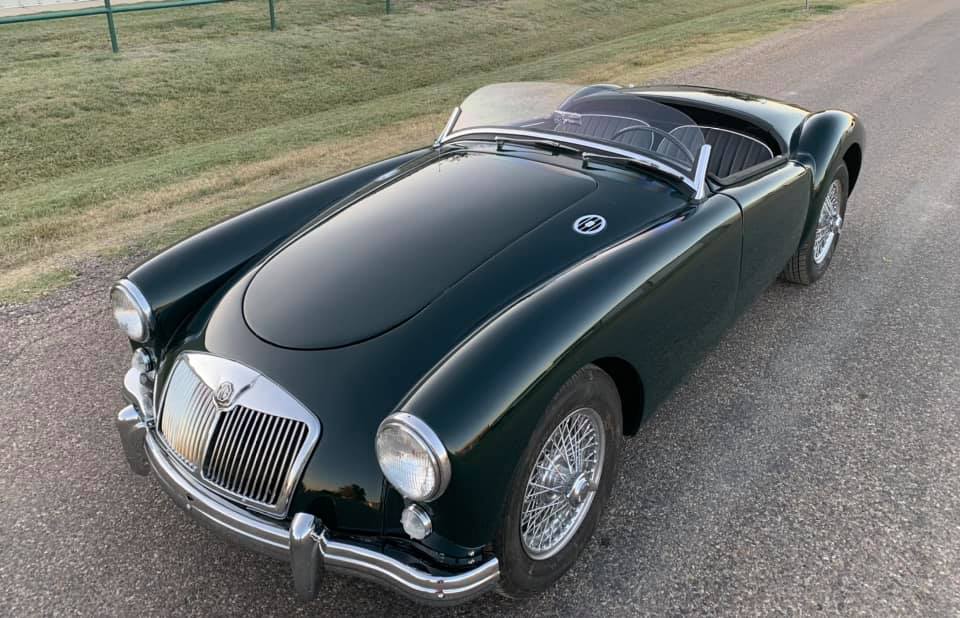
Three words: Fast, Smooth, Reliable
These goals are easy to write, but very difficult to achieve with classic cars. Countless dollars are spent each year on the old car in the garage with the promise that every time you want to drive it, it will fire up and run just like a modern car.
This may seem like a crazy idea…but, what if you could stop worrying about whether your classic will start or overheat in traffic? What if you could just turn the key and go? And what if the car actually performed better than it did before?
There are far too many classic cars sitting in garages that are pretty to look at, but would barely make it to the store.
Converting to electric can take that same car, and make it a daily-driver.
What Kind Of Cars Make Good Conversions?
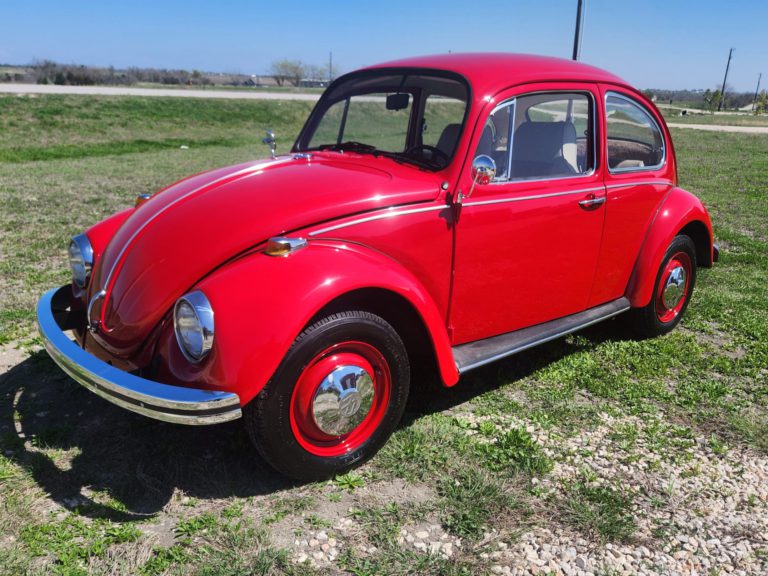
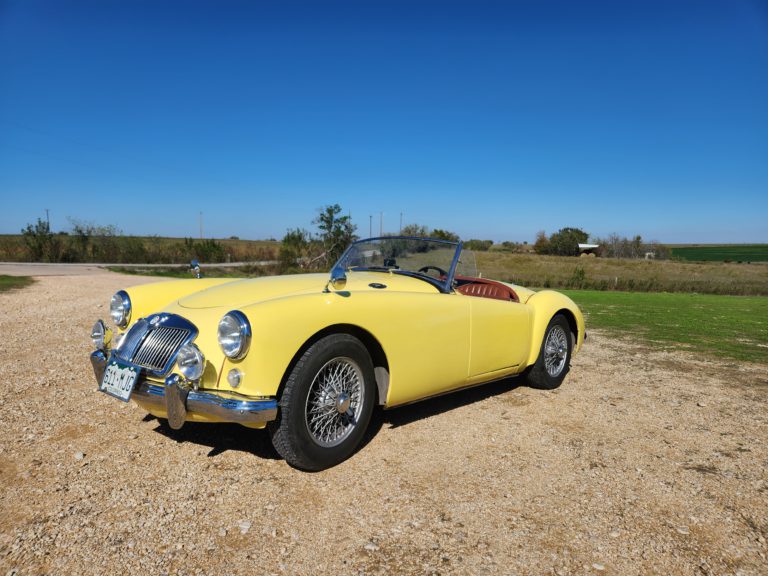
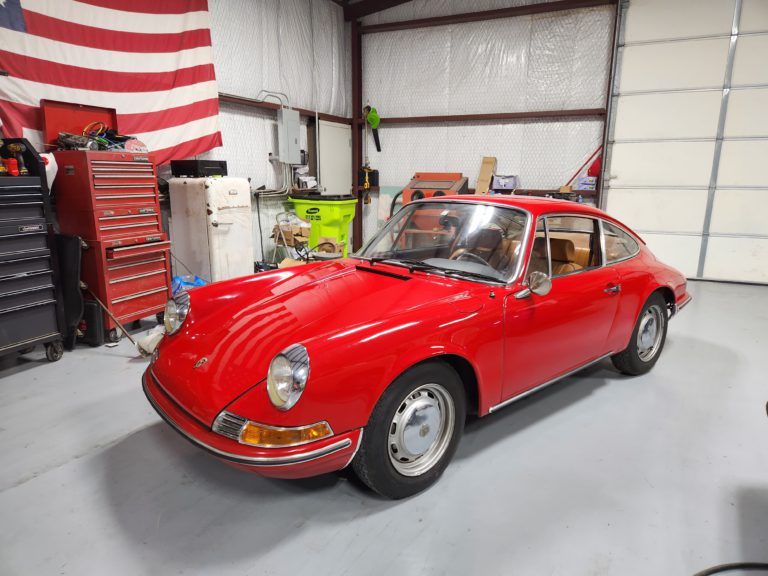
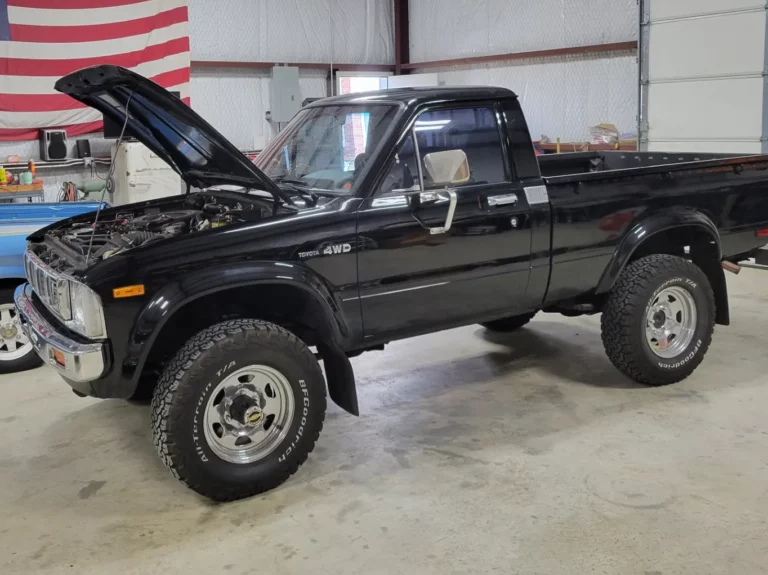
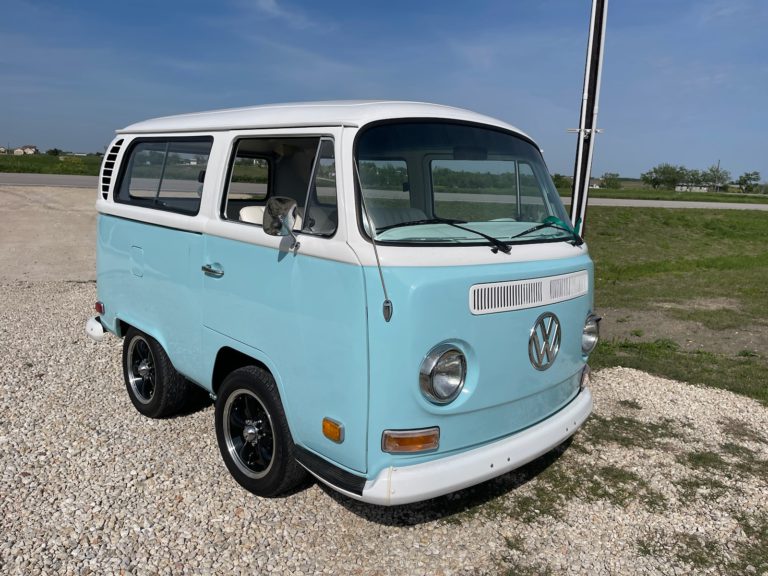
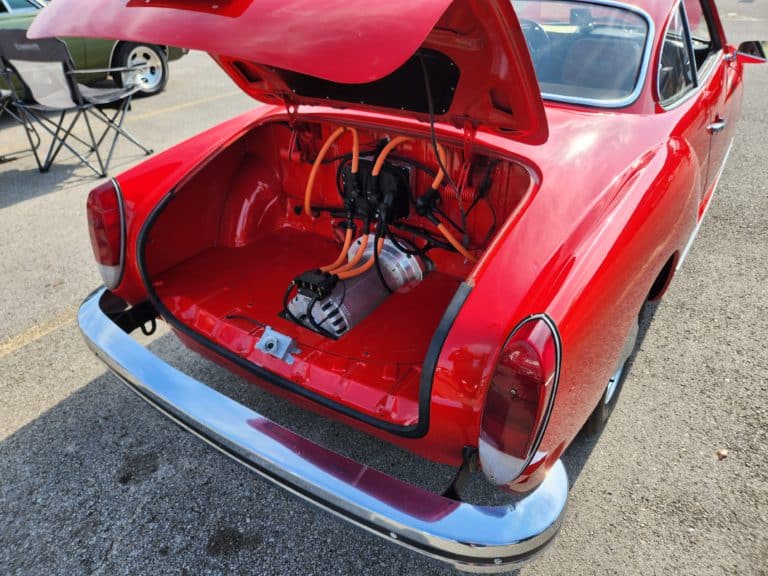
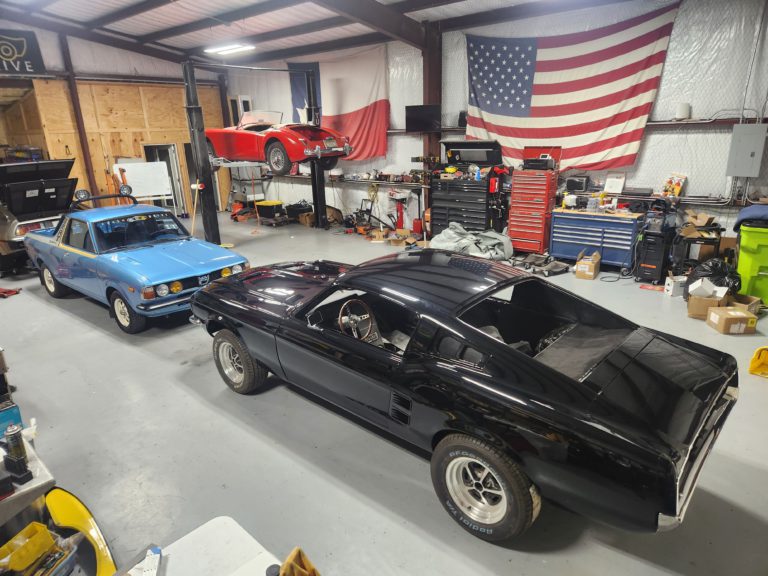
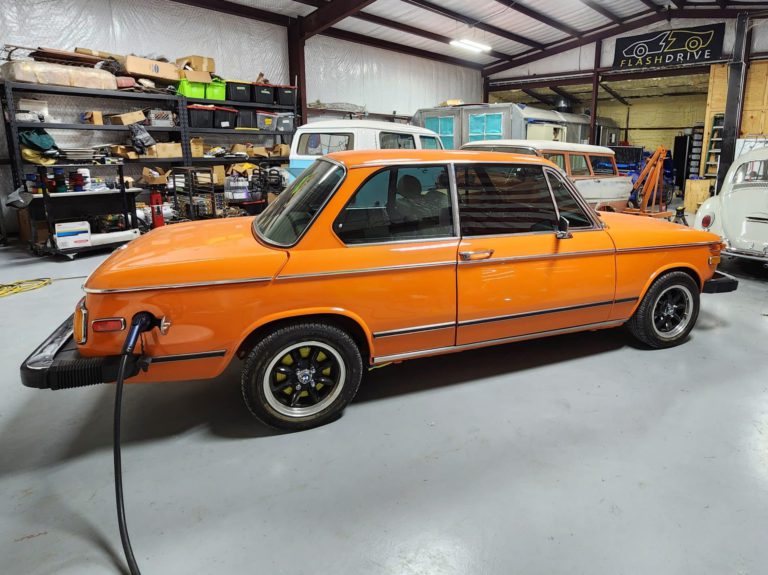
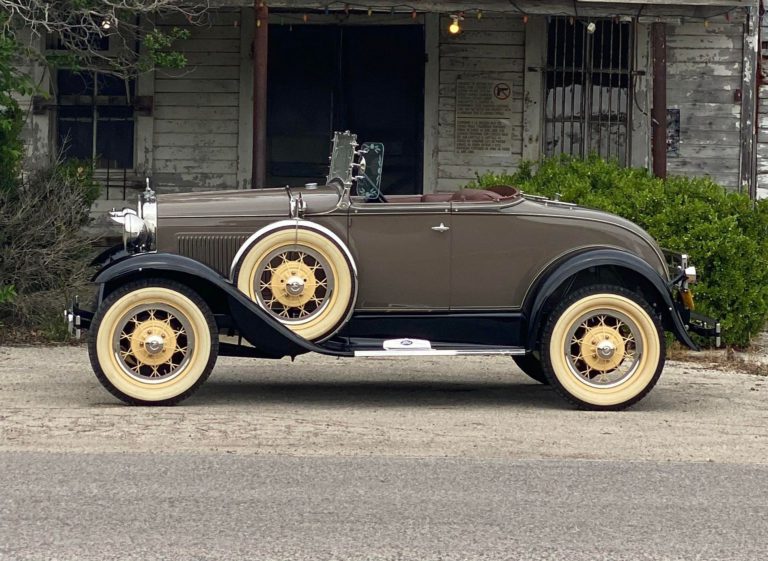
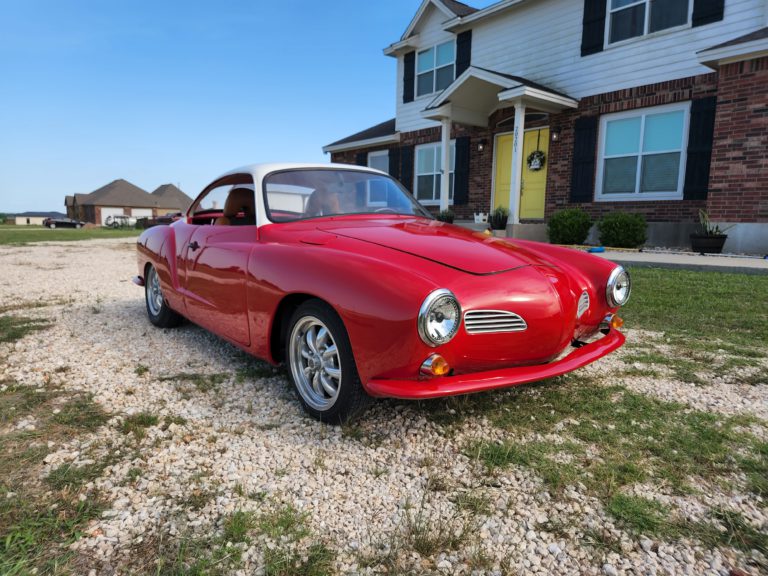
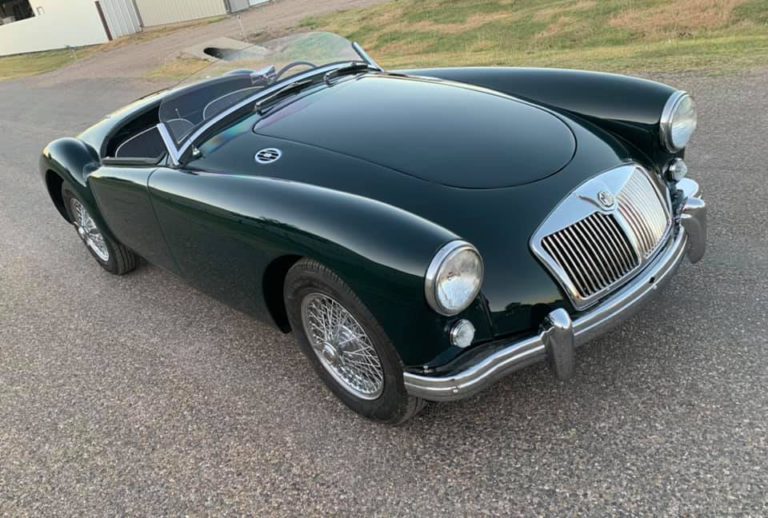
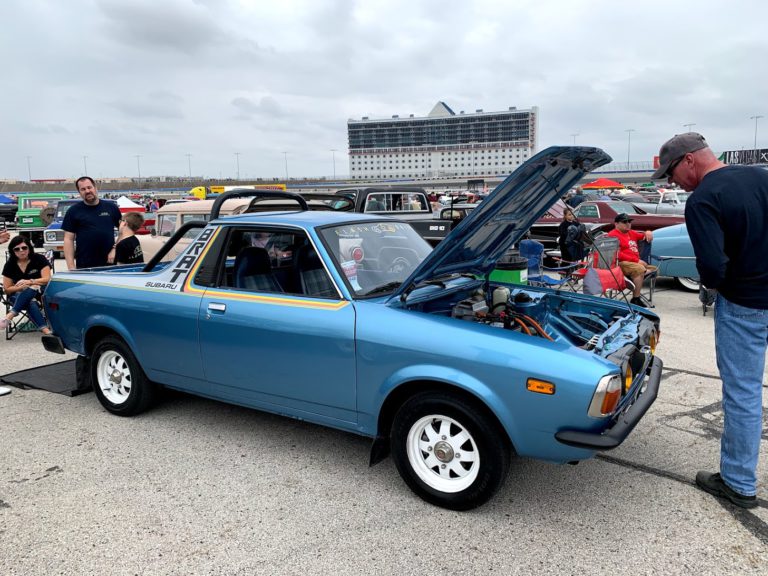
Small/Light-weight: Vehicles like classic Volkswagens (Beetle, Bus, Karmann Ghia), Fiat 500, small British sports cars (MGA, MGB, Triumph Spitfire), and BMWs are prime examples. Their lightweight bodies make them efficient candidates for electric conversions, maximizing range and performance.
Pre-1980s: Cars from before the 1980s typically feature simpler mechanical designs, making them ideal for electric conversions. Classics such as the Ford Model A, Chevrolet Bel Air, and Dodge Dart are excellent choices. Their straightforward engineering and minimal electronics simplify the conversion process, reducing complexity and costs.
Collectible: Cars with collectible or sentimental value are perfect candidates for electric conversions, as owners are often willing to invest in their preservation. Iconic models like the Porsche 911, Chevrolet Camaro, and Ford Mustang fit the bill. Converting these classics to electric not only enhances their value but also ensures their longevity in a sustainable manner.
What Makes An Electric Conversion Work?
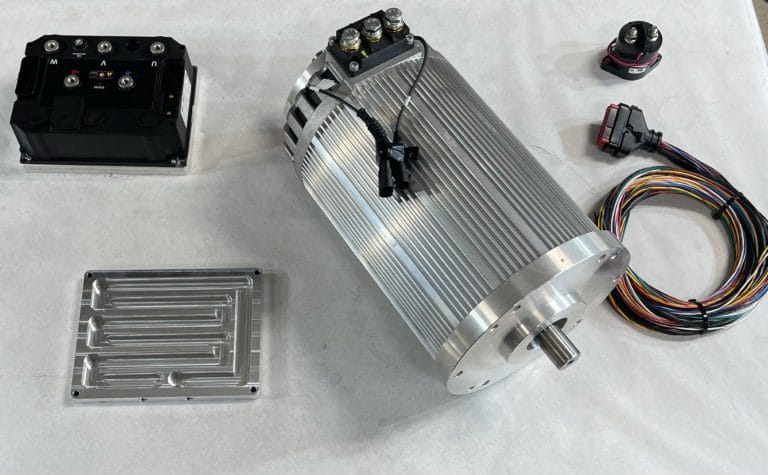
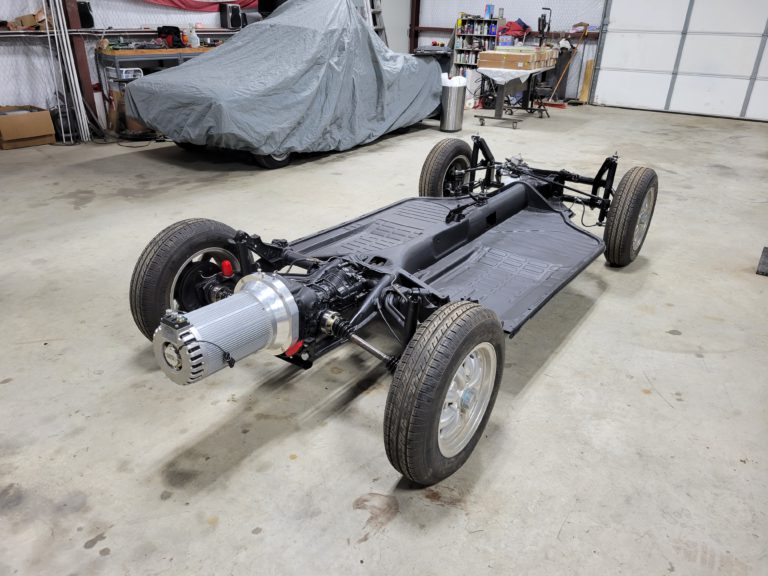
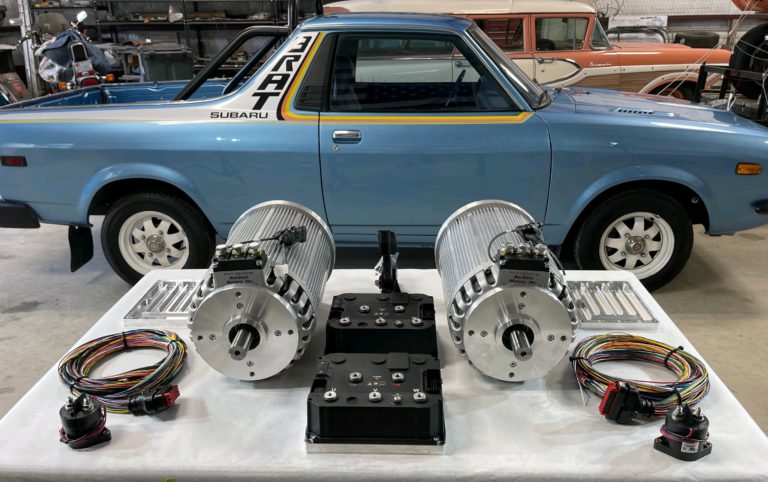
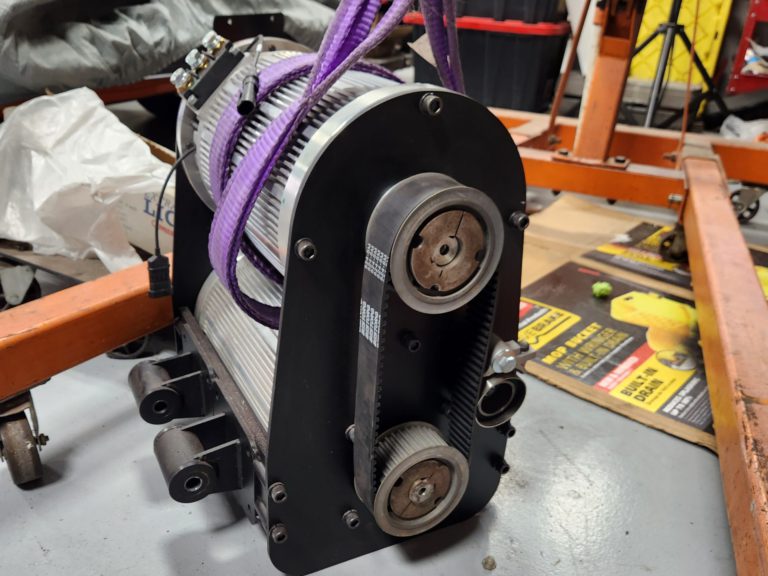
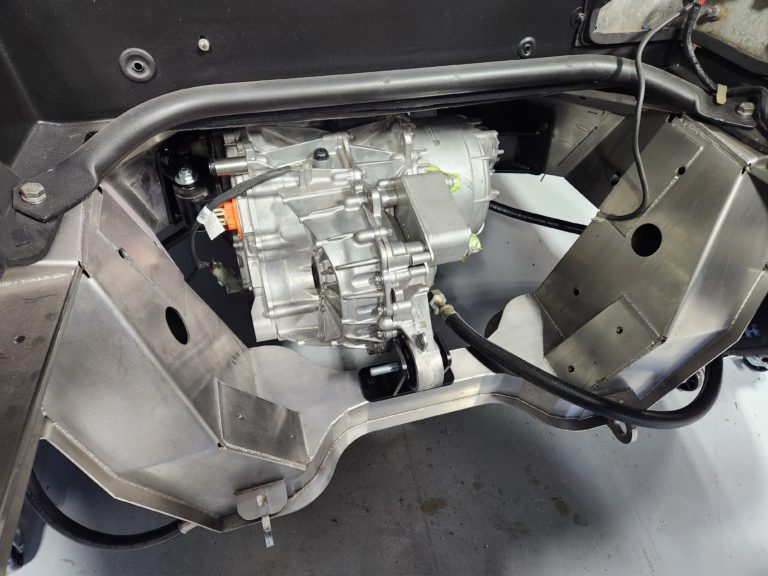
Motor
The motor is the heart of an electric vehicle, responsible for propelling the car forward. Conceptually, it operates similarly to the motor powering an RC car, albeit on a larger scale.
In today’s market, there exists a variety of motors tailored for electric vehicle applications. These motors are engineered to accommodate different input voltages and deliver a broad spectrum of power levels, catering to diverse performance needs.
Selecting the appropriate motor for a specific vehicle involves considering numerous factors, including but not limited to, the vehicle’s weight, desired acceleration, top speed requirements, and available space for motor installation. Our expertise can guide you in making an informed decision regarding the motor that best suits your vehicle’s needs.
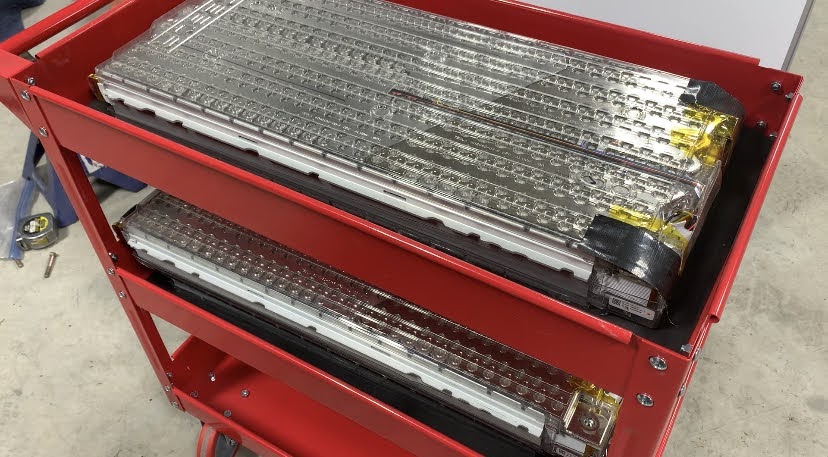
Batteries
Batteries are fundamental components in an electric vehicle conversion, responsible for storing and supplying the energy required to power the electric motor, much like a gas tank provides fuel for an internal combustion engine.
In the realm of batteries, various types with different chemistries are available, each offering unique characteristics and performance attributes. One widely favored option for many conversion projects is the Tesla battery modules. These modules stand out for their well-engineered design, integrated liquid cooling system, and impressive energy density. Additionally, their compact form factor makes them highly convenient for integration into conversion setups.
The quantity of Tesla battery modules incorporated into a typical conversion can vary, contingent upon the voltage demands of the motor. Depending on these requirements, conversions may involve anywhere from 5 to 16 modules. This variability allows for customization based on factors such as desired performance levels and available space within the vehicle.
We also offer brand new batteries as well depending on the vehicle’s intended usage.
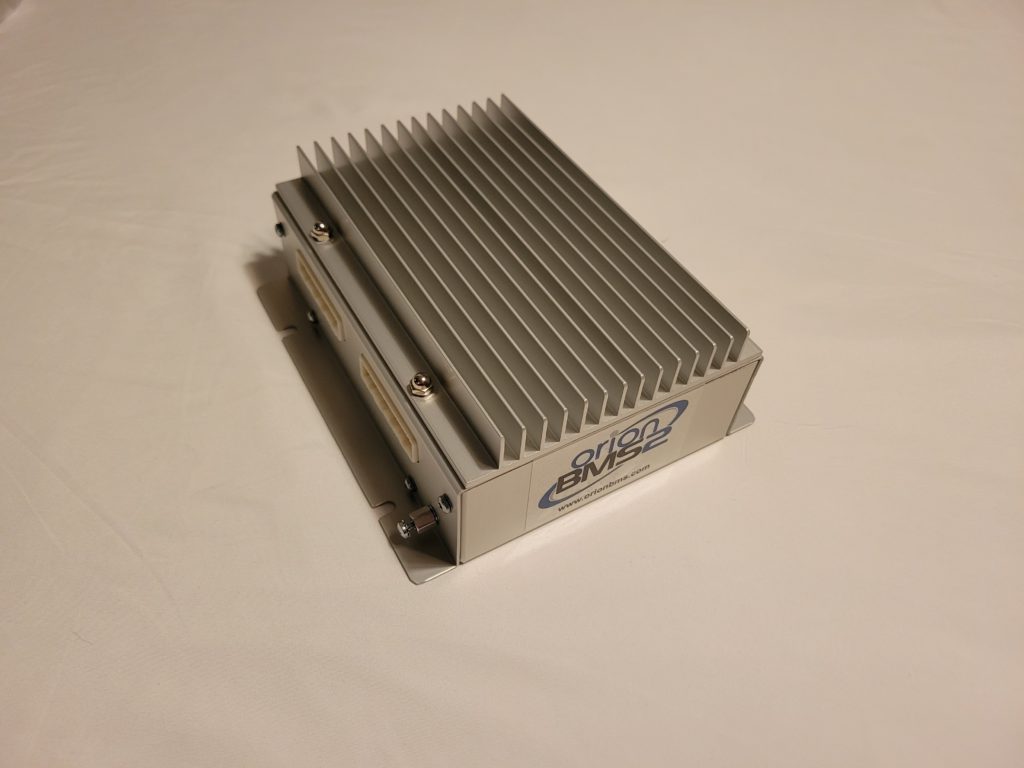
Battery Management System
A Battery Management System (BMS) is essential for an EV conversion. Its primary function is to monitor and manage the performance and safety of the battery pack.
One critical aspect of the BMS is its ability to monitor battery voltages at a cell group level. Cell groups are clusters of batteries arranged in parallel. By monitoring individual cell voltages, the BMS can identify cells that are performing poorly or have reached unsafe voltage levels. This allows the BMS to take necessary actions to limit charging and discharging of the batteries, thereby preventing overcharging, over-discharging, and other potentially hazardous conditions.
In addition to voltage monitoring, the BMS also monitors battery temperatures. Maintaining batteries within a safe temperature range is crucial for their performance and longevity. Many BMS systems are equipped to control the cooling and heating systems of the battery pack to ensure that temperatures remain within optimal limits.
Furthermore, some advanced BMS units, like the Orion BMS mentioned, offer additional features such as communication interfaces with charging stations. This enables seamless integration with charging infrastructure, allowing for efficient charging and communication between the battery pack and external charging systems.
Overall, the BMS plays a critical role in ensuring the safety, performance, and longevity of the battery pack in an EV conversion.
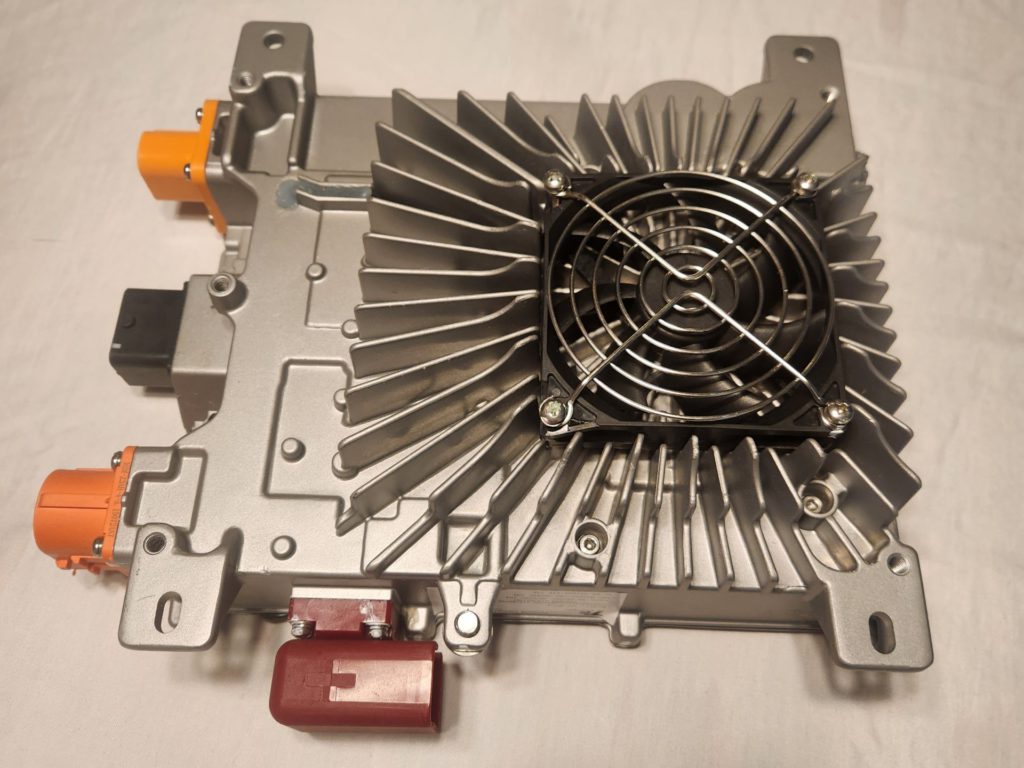
On Board Charger
The on-board charger is responsible for the actual charging of the high voltage battery pack in an electric vehicle. It’s important to note that this is often confused with a charging station, which provides the power that the charger will use to charge the batteries. The on-board charger is installed within the vehicle itself.
The Battery Management System (BMS) plays a crucial role in controlling the charger. It manages the charging process and regulates the amount of power that the charger will provide to the batteries. This helps ensure safe and efficient charging.
Chargers come in various sizes, and it’s essential to match the charger size to the maximum voltage of the system and the amperage of the charging stations. For an EV conversion, a typical charger size ranges from 3.3 kW to 6.6 kW, although larger sizes may be used depending on the specific requirements of the conversion and the available charging infrastructure.
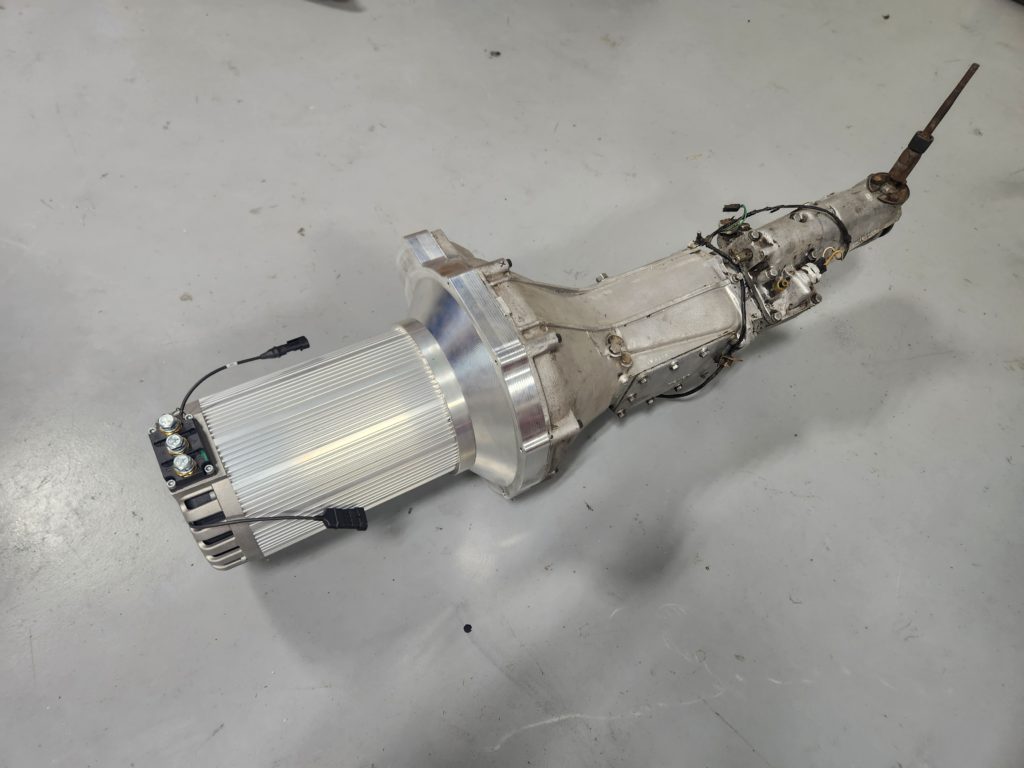
Transmission with an EV Conversion?
Electric vehicle conversions often utilize transmissions from the donor vehicle for various reasons, primarily to simplify the conversion process and leverage existing engineering. Unlike original equipment manufacturer (OEM) electric cars, which typically do not have transmissions, classic EV conversions may retain the stock transmission.
By keeping the stock transmission, the rest of the drivetrain remains intact, requiring fewer modifications to the vehicle’s original design. This can save time and resources during the conversion process and allows for a smoother integration of the electric motor into the vehicle’s drivetrain.
While the basic operation of the converted vehicle may resemble that of an OEM electric car (i.e., press accelerator to go, brakes to stop), retaining the clutch and gears provides additional options. For instance, drivers can shift gears for higher speeds or participate in impromptu speed contests, adding a level of versatility to the driving experience.
In some cases, particularly when using larger motors like those from Tesla, the need for a transmission may be eliminated. Instead, the motor can directly connect to the wheels via CV axles. This setup simplifies the drivetrain and can be more efficient for certain applications.
Overall, the inclusion of transmissions in classic EV conversions offers benefits such as simplified integration, flexibility in driving, and compatibility with different motor sizes.
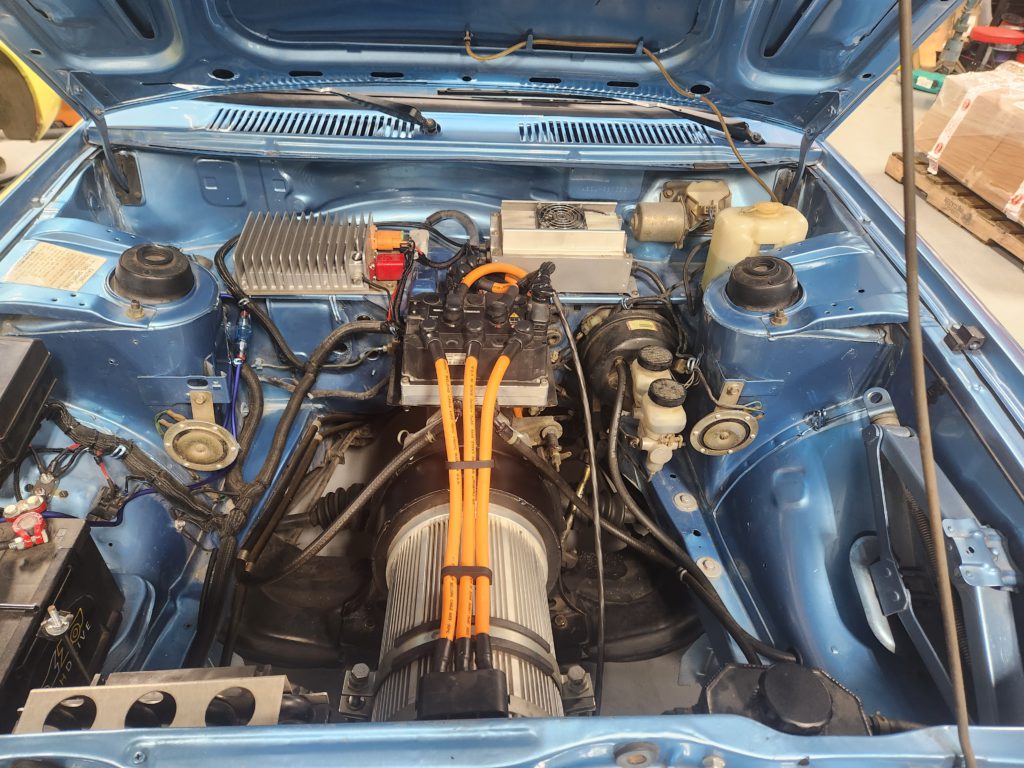
Is There Still a 12V Battery?
In an EV conversion, it’s common for a 12V battery to be present, performing several essential functions.
Firstly, the 12V battery powers the chassis wiring, including headlights, turn signals, and other basic electronics. These components require a separate power source from the main traction battery used to drive the electric motor.
Additionally, the 12V battery plays a crucial role in “boot-strapping” the system. It initiates the activation of EV components, allowing them to take over once the vehicle is powered up.
To ensure the continuous operation of the 12V system, a specialized component called a DC-DC converter is installed. This converter is responsible for keeping the 12V battery charged, akin to the role of an alternator in traditional internal combustion engine vehicles.
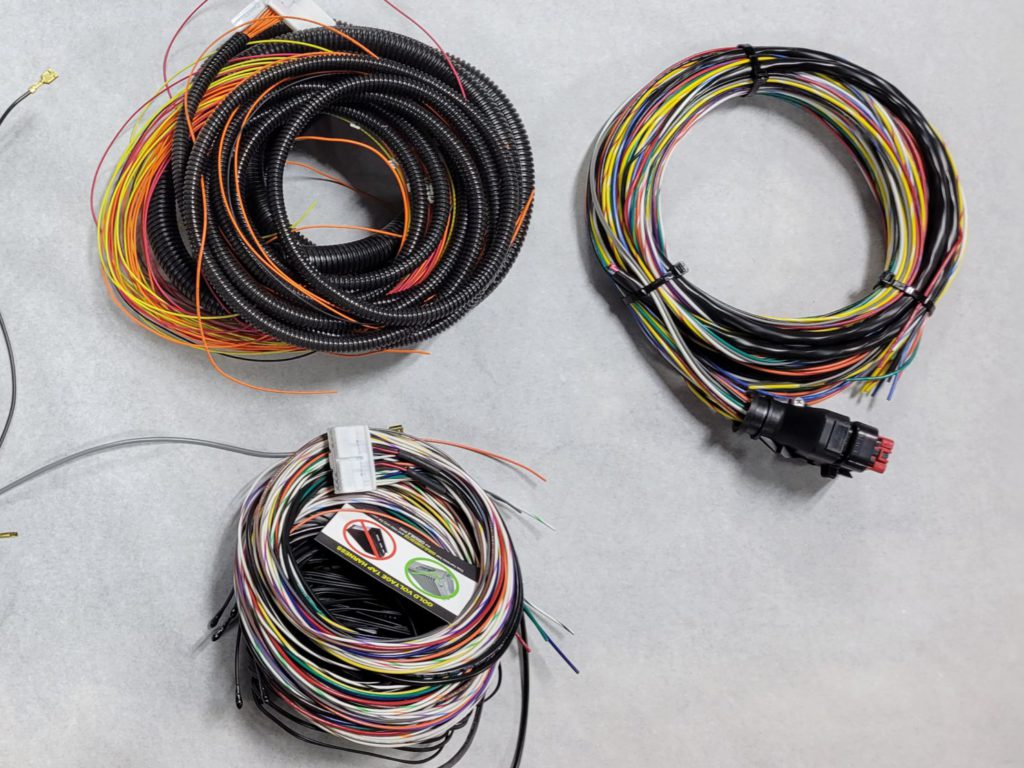
Wiring
EV conversion entails a substantial amount of wiring, constituting a significant portion of the conversion process.
From managing high voltage wiring, fuses, contactors, cell taps, controllers, chargers, and BMS to handling the essential 12V chassis wiring, the task can appear daunting to many.
However, through our extensive experience in completing numerous conversions, we’ve developed a solution known as the “JIB” (Junction Interface Box). This innovative product streamlines the interconnection between various components, simplifying the wiring process and enhancing efficiency.
The JIB serves as a central hub for managing connections between different components, facilitating monitoring and ensuring the 12V battery remains charged when the vehicle is not in use. With the JIB, we’ve optimized the conversion process, making it more accessible and less intimidating for enthusiasts and professionals alike.
Charging Interface
Charging is as easy as plugging it in!
We use the standard J1772 charging port. This allows you to charge at home or public charging stations.
We also now support the Tesla (NACS) charging port for Level 2 AC charging!
We can also support DC fast charging (CSS) on higher voltage systems, such as a Tesla swap.
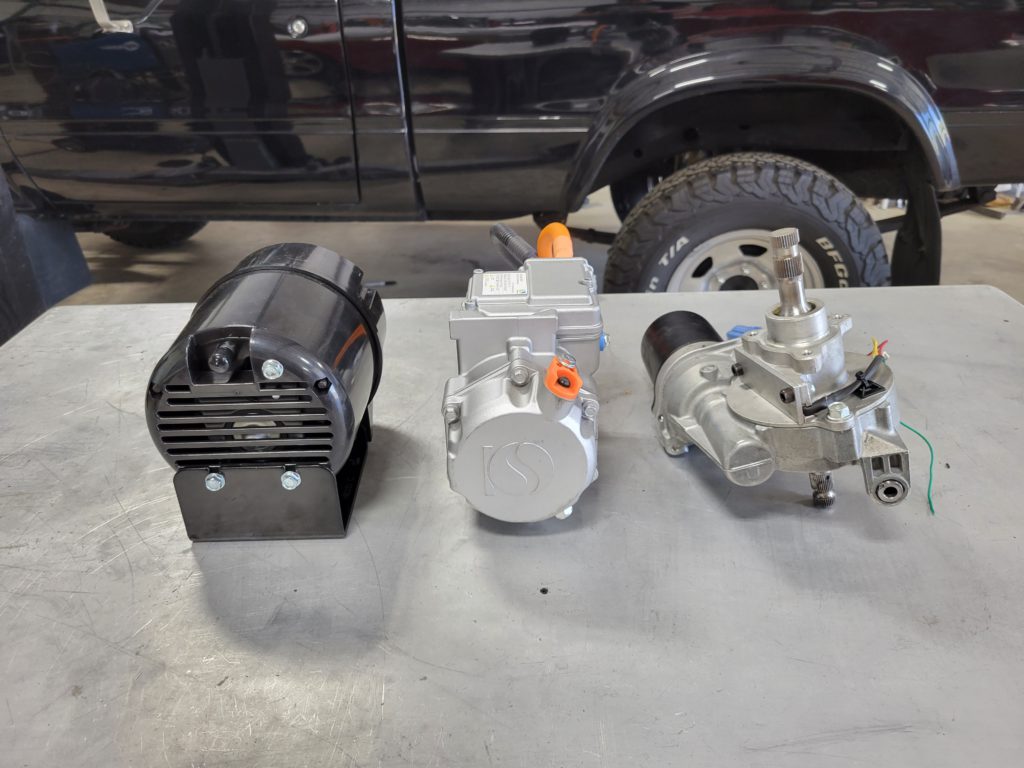
Accessories
Air Conditioning (AC): By utilizing an electric AC compressor and controller, the functionality of air conditioning can be maintained without relying on a gasoline engine. This is a common feature in modern electric vehicles, ensuring occupants can still enjoy climate control comfort.
Power Brakes: Traditionally, power brakes rely on engine vacuum to assist in braking. In electric vehicles, this vacuum is not available. However, solutions like using a vacuum pump or electric booster can be employed to provide the necessary assistance, maintaining the familiar feel of power brakes.
Power Steering: Similarly, power steering traditionally uses hydraulic fluid, which may not be needed or preferred in electric vehicles. Electric Power Assist Steering Units (EPAS) provide an alternative that offers adjustable levels of assistance without the need for hydraulic fluid. EPAS systems are quieter and can enhance the driving experience.
How Do We Get Started?
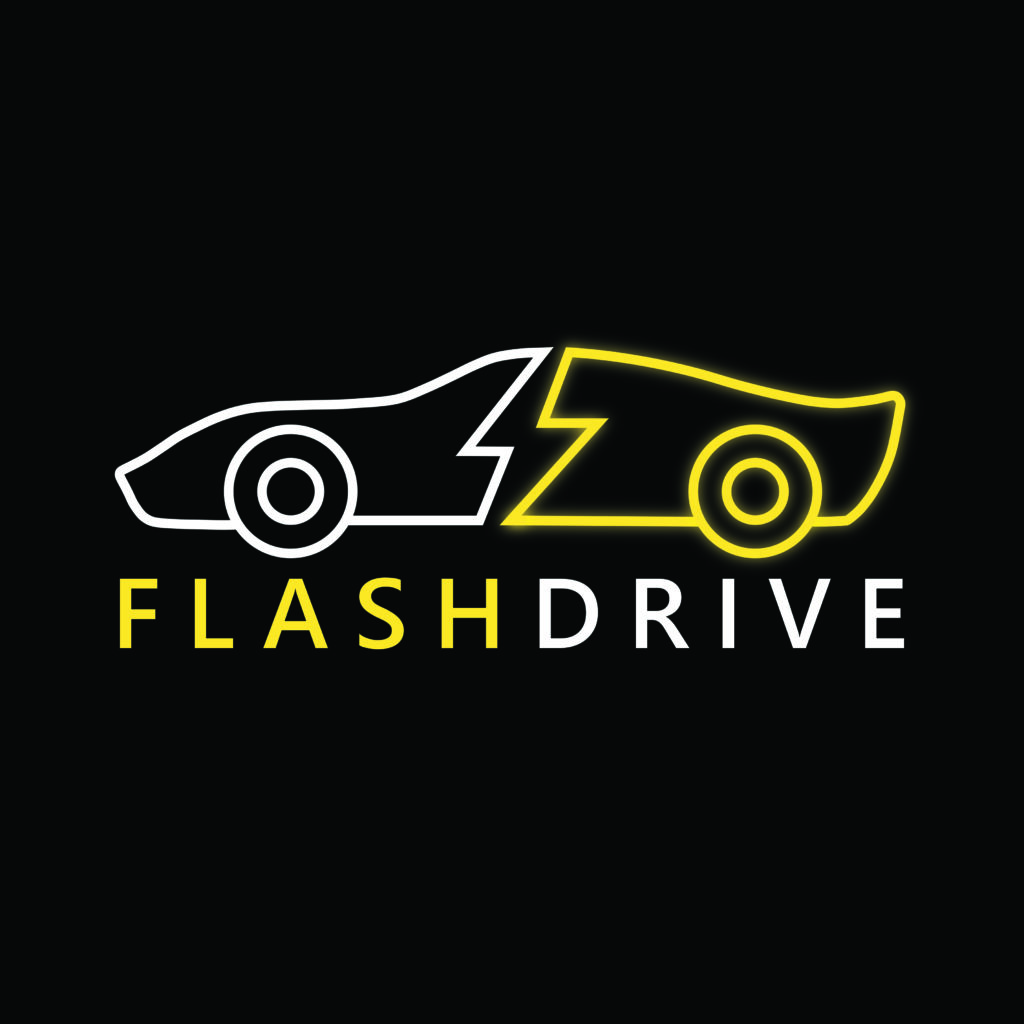
Flash Drive Motors
We offer turn-key conversions of your classic car and DIY EV Conversion kits for those looking for a fun and rewarding project.